When it comes to 3D printing, the possibilities are virtually endless. You can create objects using a wide range of materials, known as 3D printing material types, ranging from chocolate to titanium. However, determining the best material for your specific project can be a challenging task. To ensure optimal results, it’s essential to familiarize yourself with the available options and understand the characteristics of different 3D printer material types. Considering that materials comprise a significant portion of your 3D printing investment, conducting thorough research beforehand will prove beneficial.
At All3DP, we offer an extensive collection of guides on 3D printing material, covering everything from carbon-fiber-infused filaments to nylon powders. Our team constantly prints, tests, and compares various materials, catering to everyone from novice home hobbyists to experienced engineers seeking to enhance industrial components. Whether you’re searching for the ideal filament or the most suitable resin, our concise guide will assist you in selecting the perfect 3D printing material for your next project or elevating the quality of your prints.
Understand Material Formats: Filament, Resin, Powder, Pellets, Wire, Paste, Gel
FILAMENT
The fused deposition modeling (FDM) printer has long been the preferred and cost-effective method for 3D printing, making it incredibly popular among enthusiasts. With FDM technology, you have a wide variety of options when it comes to types of 3D printing materials. From PLA and ABS to flexible filaments and even composite materials, there is a diverse range of materials available to suit different project requirements.
1. PLA: All-Rounder

PLA, short for polylactic acid, is one of versatile and popular 3D printing materials. It is affordable, easy to print with, and compatible with most FDM printers.
2. ABS: Rock-Hard
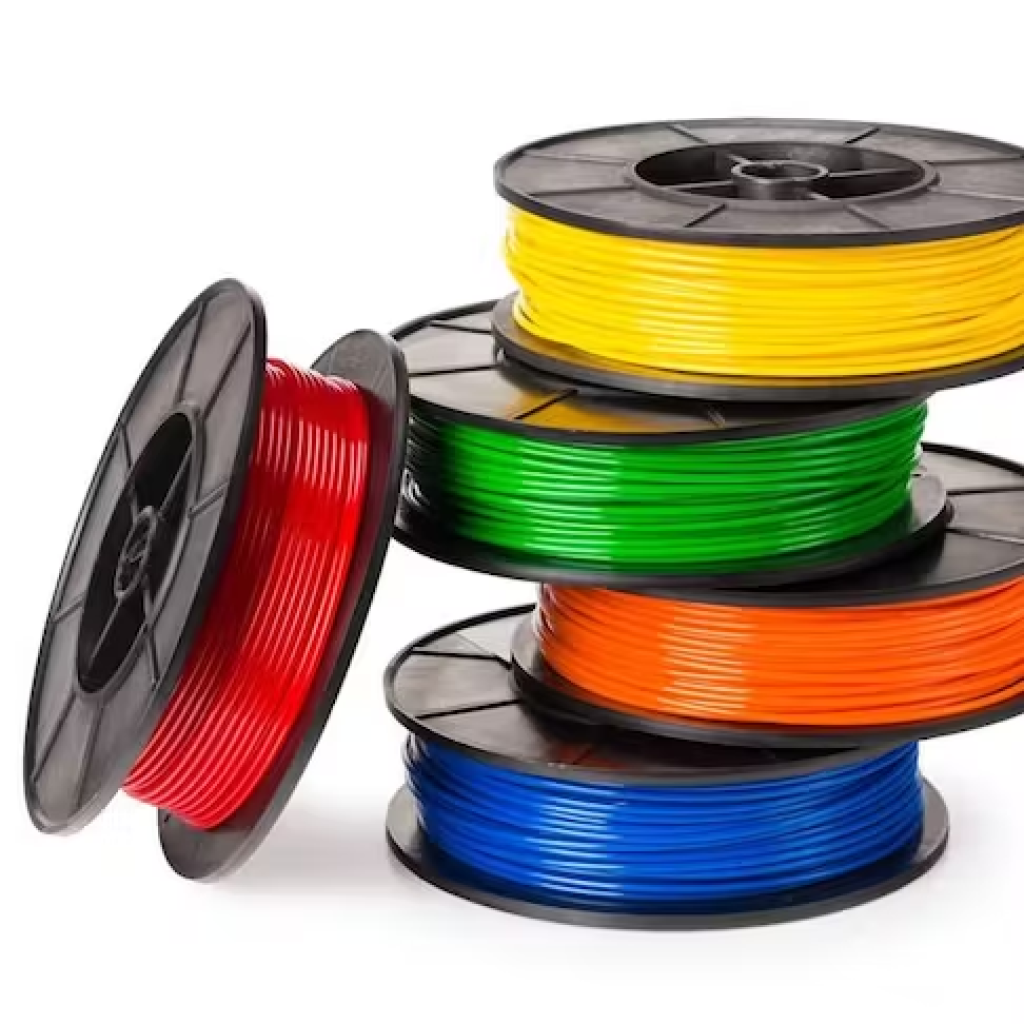
ABS (acrylonitrile butadiene styrene) is a widely used 3D printer material known for its durability, strength, and temperature resistance.
3. PETG: Food-Safe
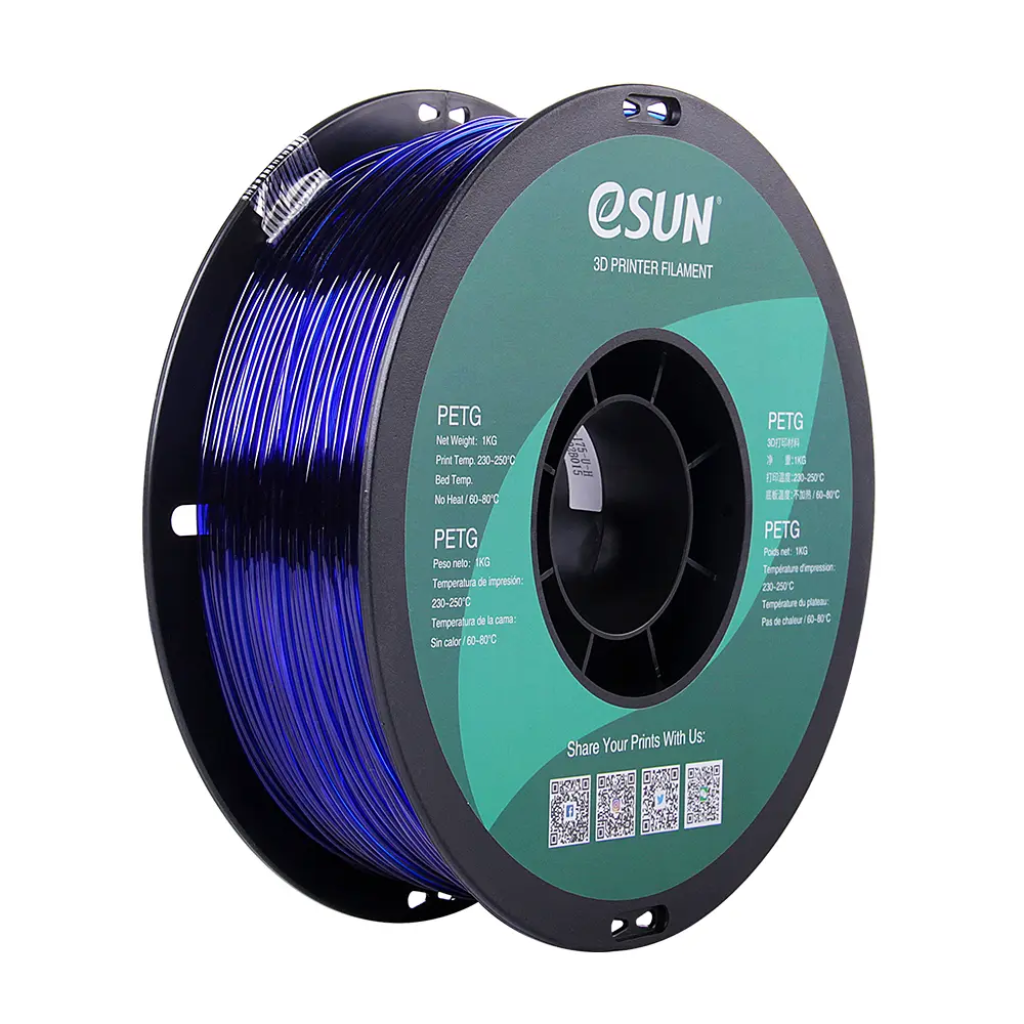
PETG, derived from polyethylene terephthalate, is a filament known for its strength, durability, and transparency. It offers good layer adhesion and is less complicated to print than ABS.
4. TPU, TPE, TPC: Flexible
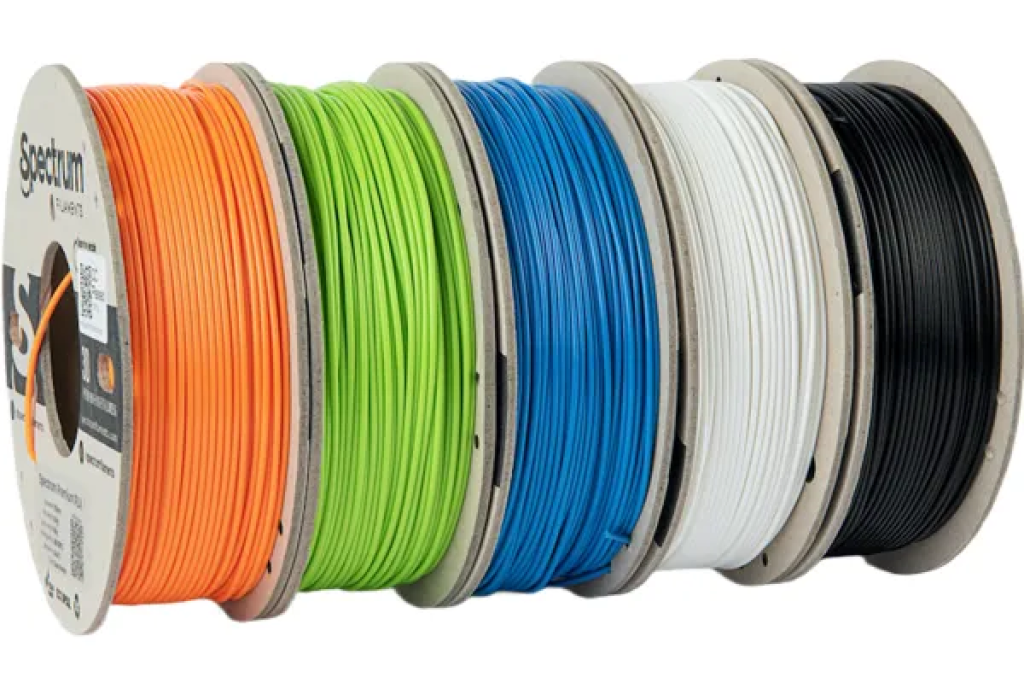
TPU (thermoplastic polyurethane), TPE (thermoplastic elastomer), and TPC (thermoplastic co-polyester) belong to the family of flexible materials. These blends of plastic and rubber are widely used to create parts that can be bent or stretched without deformation.
5. Nylon: Tough & Durable
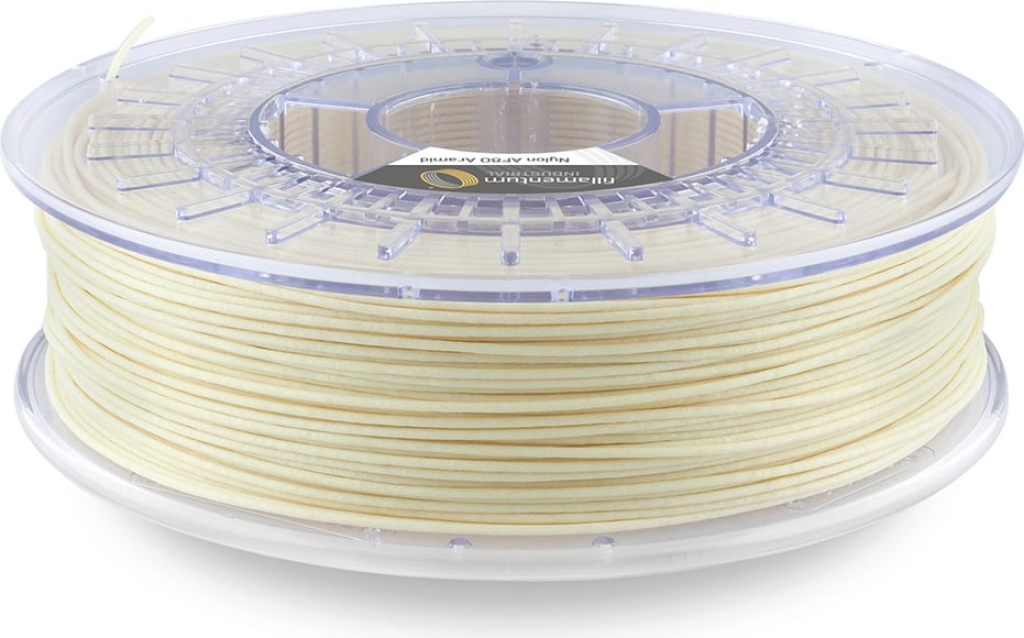
Nylon, also known as polyamide (PA), is a strong and durable material used in various applications. It offers good tensile and mechanical strength, as well as resistance to high temperatures and impacts.
6. ASA: Sunlight Resistant
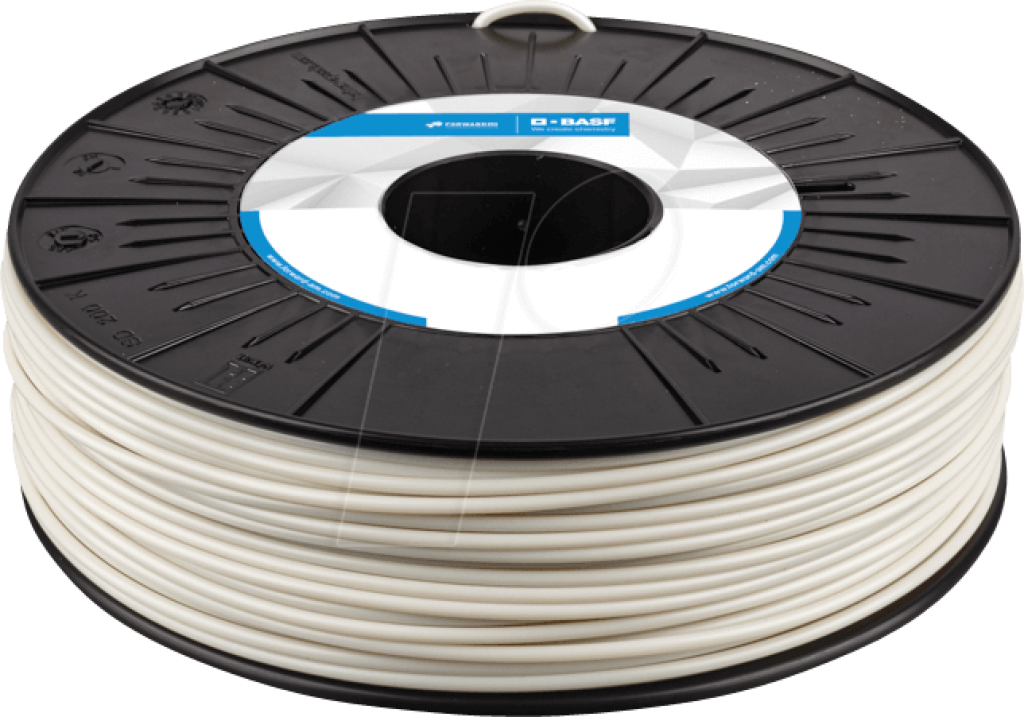
ASA (acrylonitrile styrene acrylate) is a material known for its high impact strength, chemical resistance, and UV stability. ASA is easier to print compared to ABS but still requires high extruder and bed temperatures.
7. PVB: Smooth & Clear

PVB (polyvinyl butyral) is a specialty filament that can be layer smoothed using Isopropyl Alcohol. It is a safer alternative to ABS for layer smoothing, which typically requires acetone.
8. HIPS: High-Impact
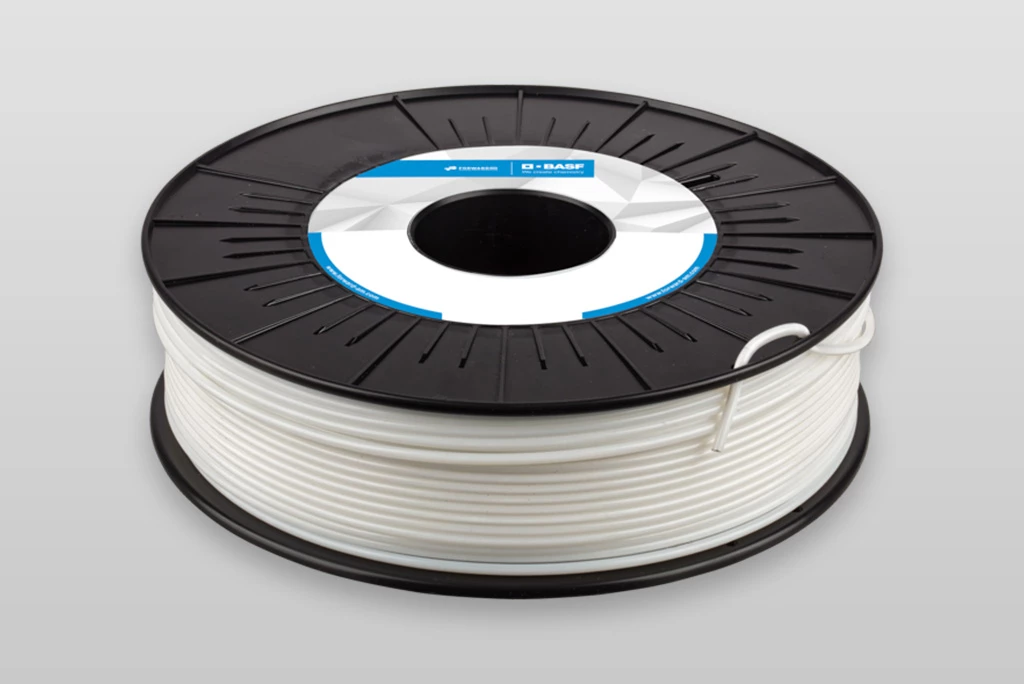
HIPS (high impact polystyrene) is a material blend of polystyrene plastic and polybutadiene rubber.
9. PVA: Water Soluble
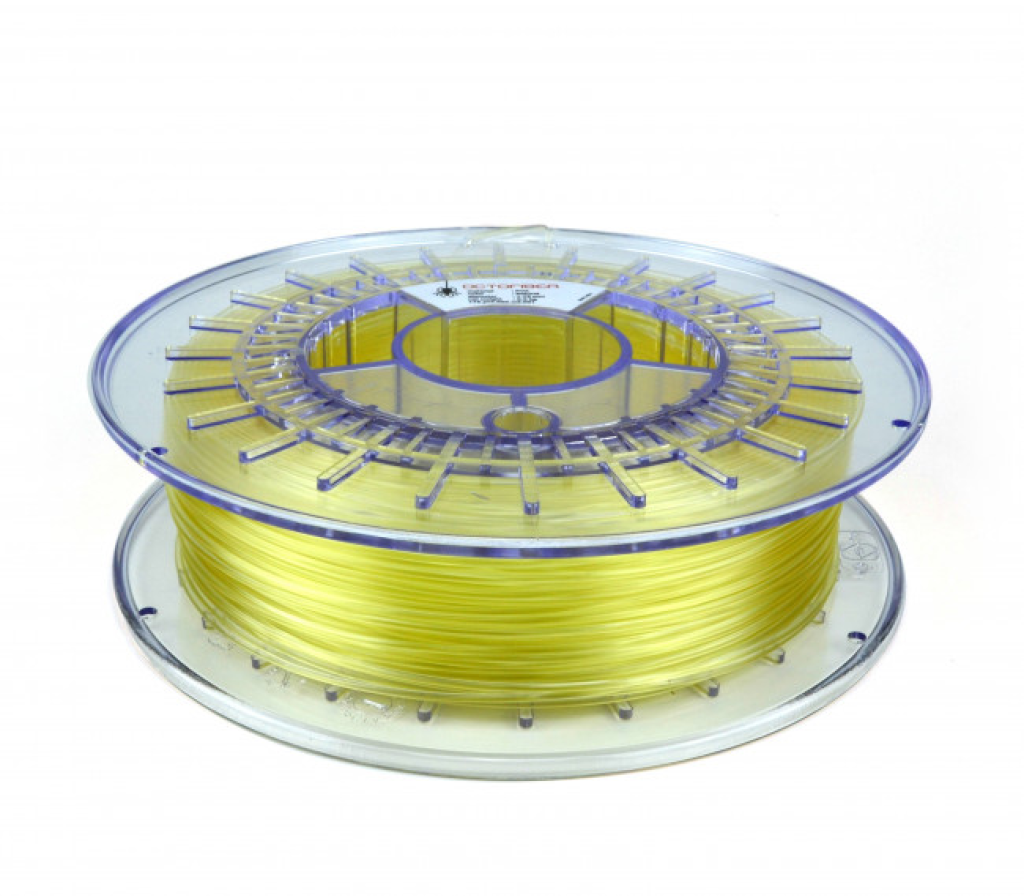
PVA (polyvinyl alcohol) is a water-soluble filament used primarily as a support material in dual extrusion 3D printing.
10. Conductive & ESD-Safe
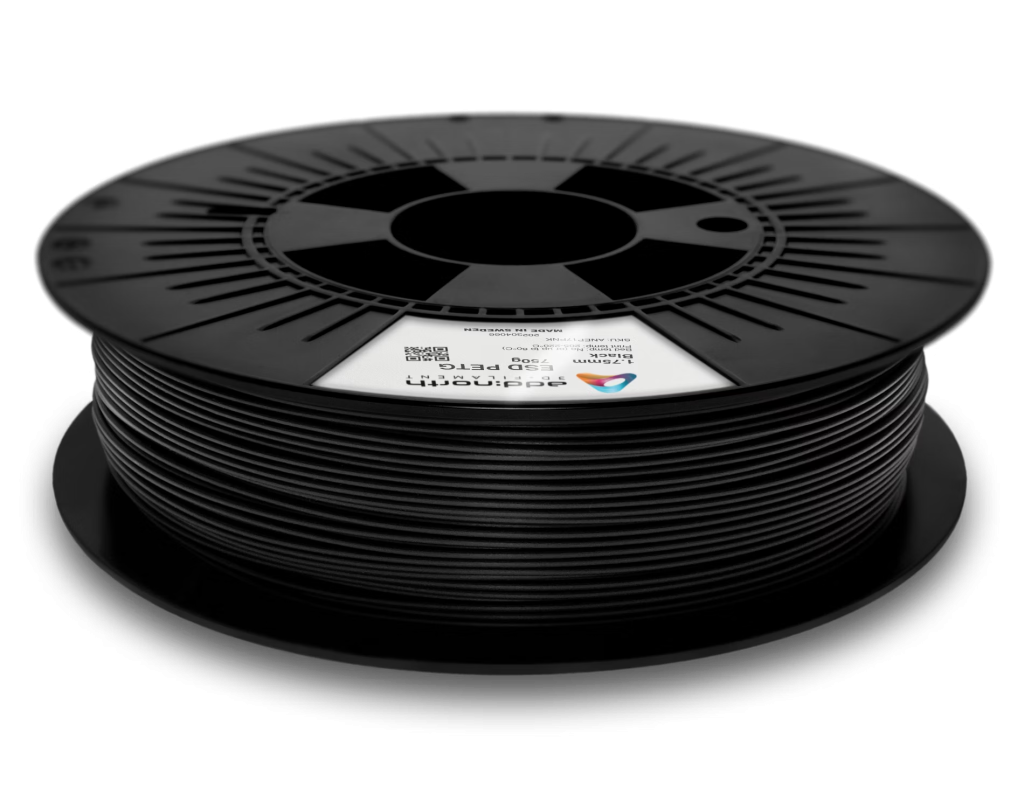
Conductive 3D printer filaments are infused with conductive carbon particulates, enabling them to conduct electricity. ESD-safe materials protect electronics from electrostatic discharge and are used for housings, fixtures, and tools.
11. Wood Composite
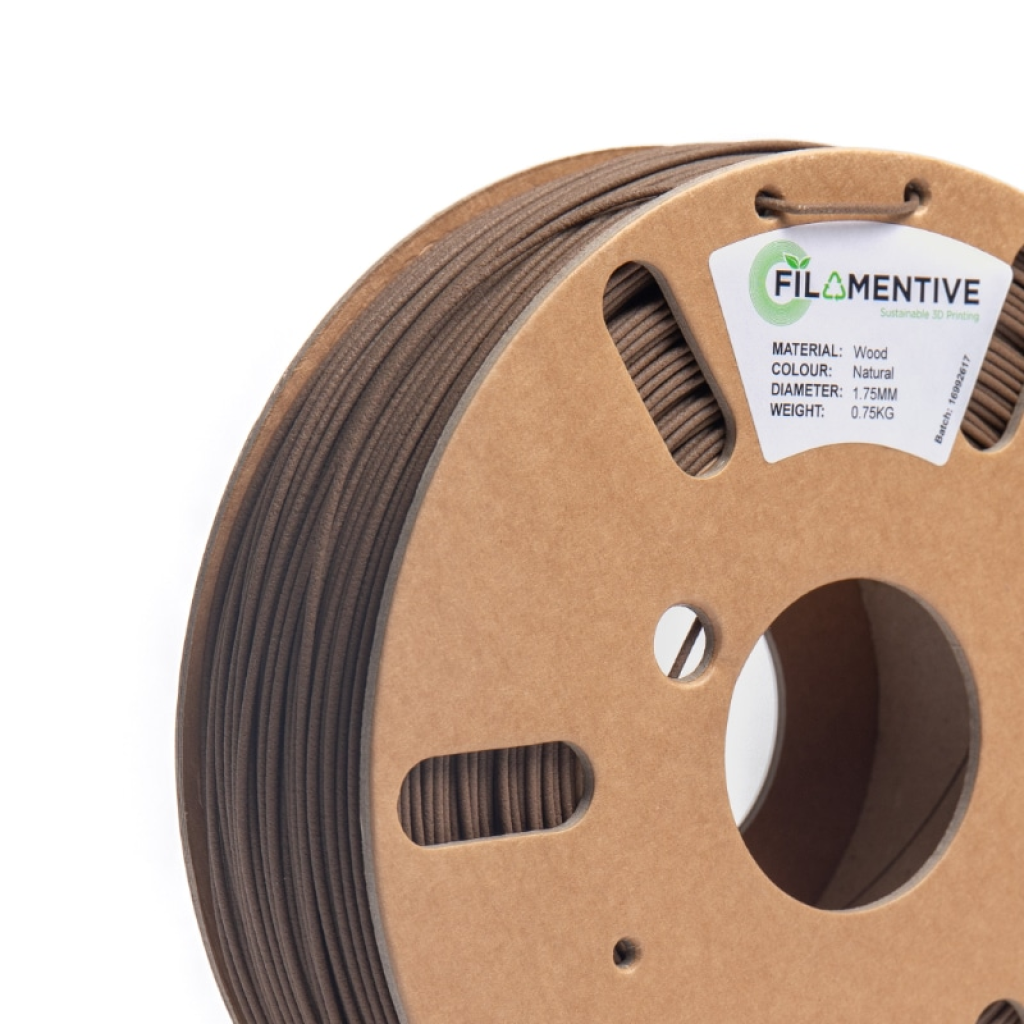
Wood composite filaments are typically PLA infused with wood fiber, offering a unique aesthetic appeal and tactile experience.
12. Metal Composite
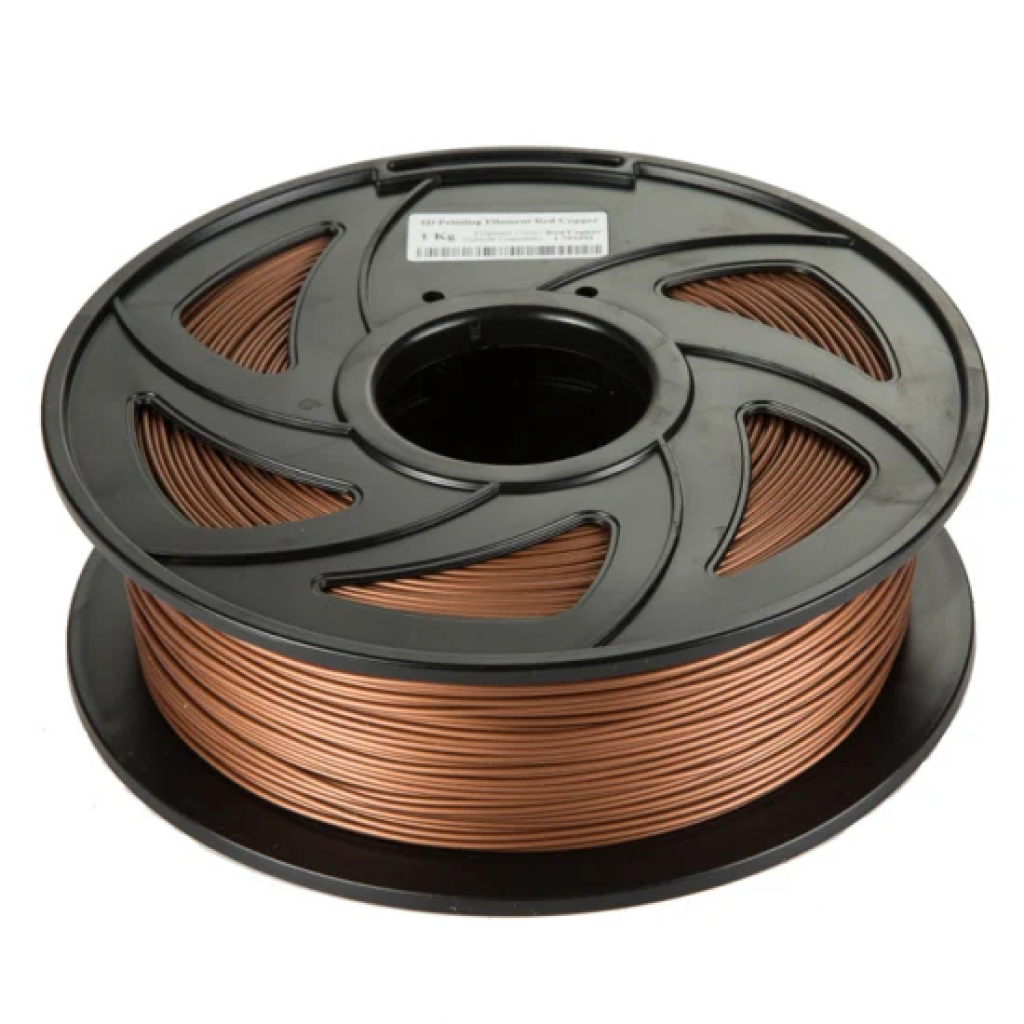
Metal composite filaments provide the appearance of metal when polished but do not possess the functional properties of metal.
13. PC: Heat Resistant
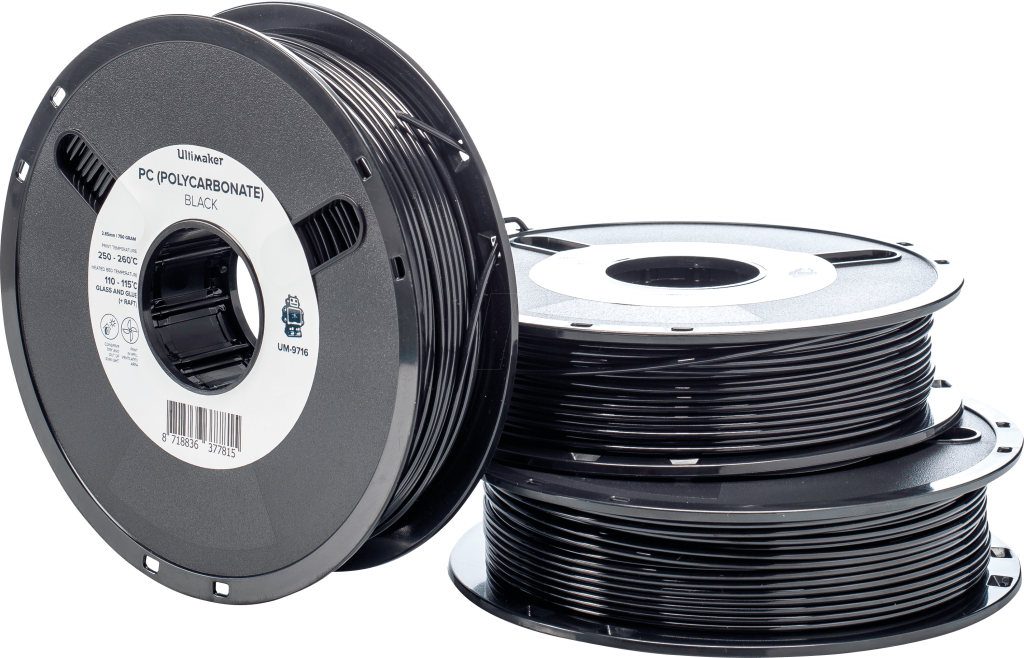
Polycarbonate (PC) is a strong and heat-resistant material known for its optical clarity and toughness.
14. PEI: High Strength-to-Weight Ratio
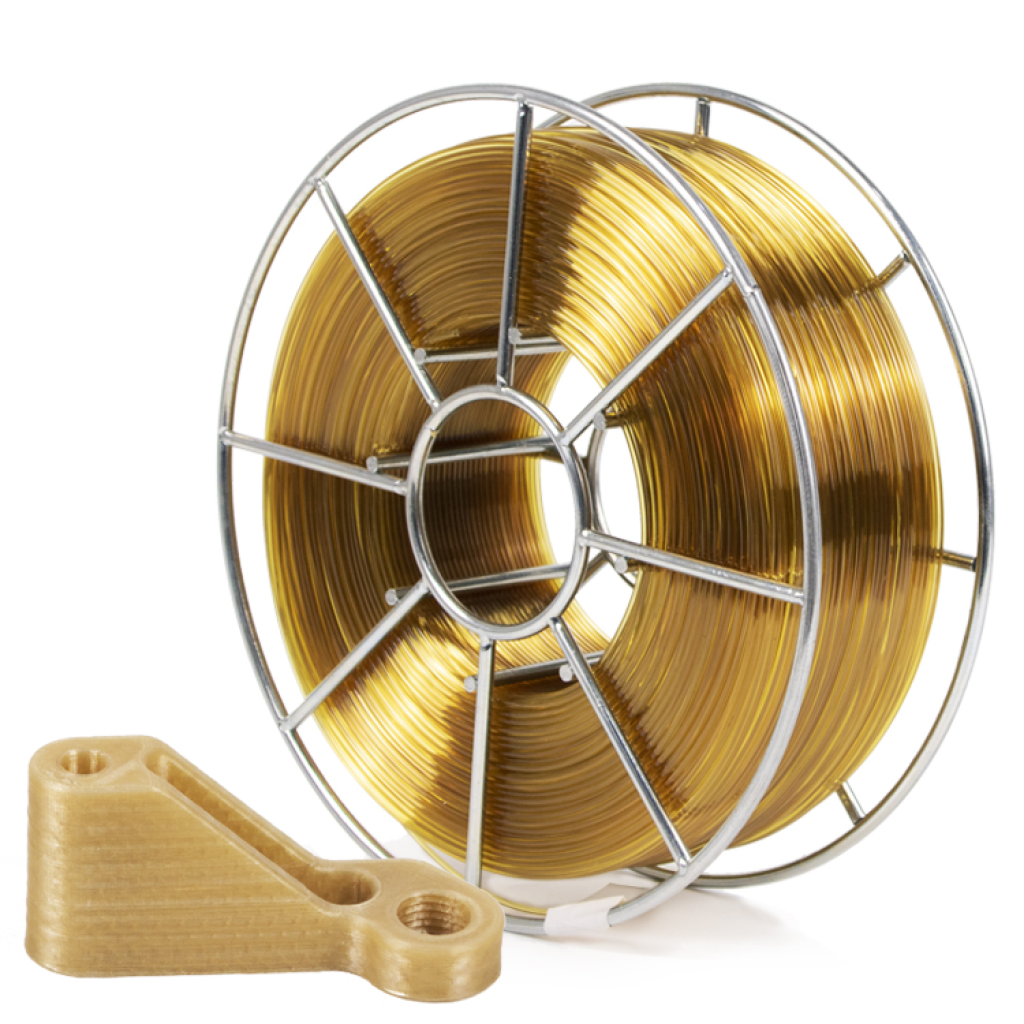
PEI (polyetherimide) is a high-performance plastic offering excellent thermal, mechanical, and electrical properties. It has a high strength-to-weight ratio, making it a cost-effective alternative to metal.
15. PEEK: Lightweight Metal Replacement
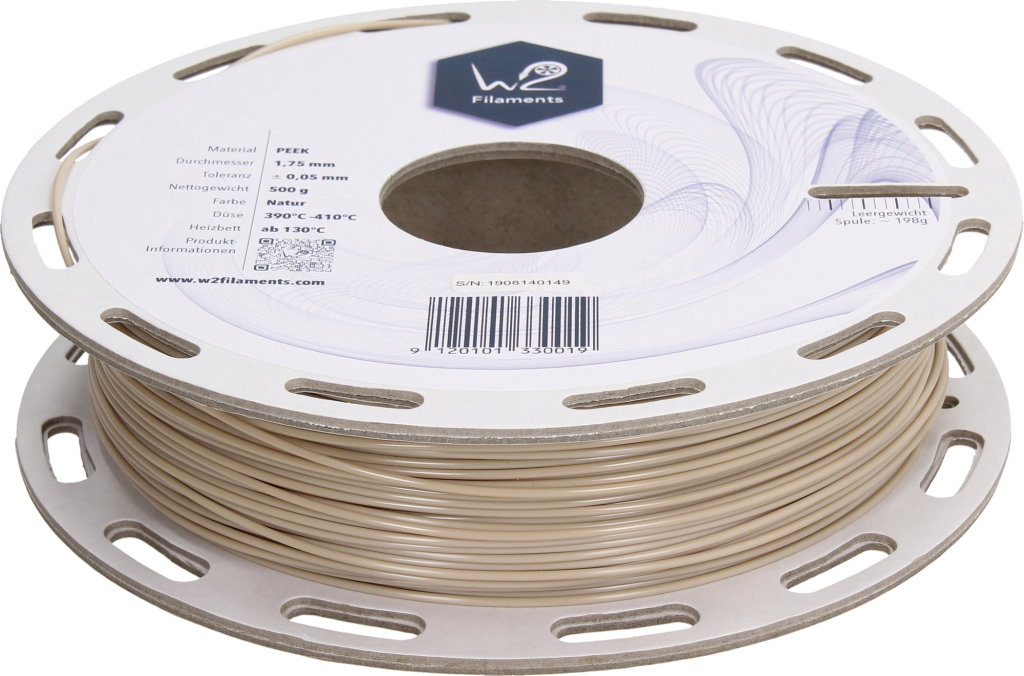
PEEK (polyetheretherketone) is a high-performance polymer known for its excellent mechanical, thermal, and chemical resistance properties. It is lightweight compared to metal.
16. PEKK: Stiff & Strong
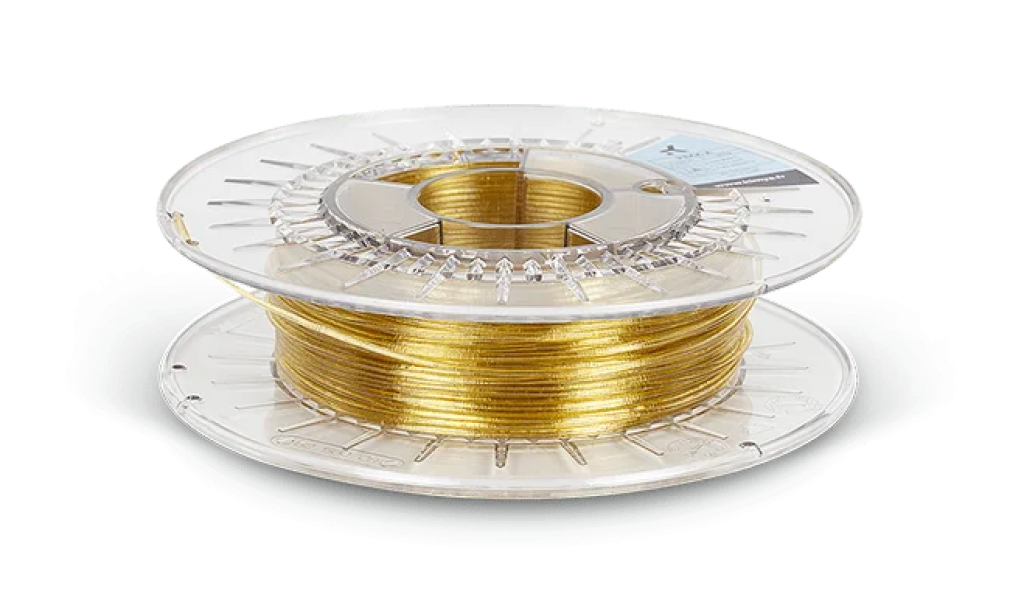
PEKK (polyetherketoneketone) is a high-performance polymer with exceptional mechanical, thermal, and chemical resistance properties. It is easier to print compared to PEEK and offers excellent dimensional accuracy and z-strength.
17. PVDF: Resists Extreme Conditions
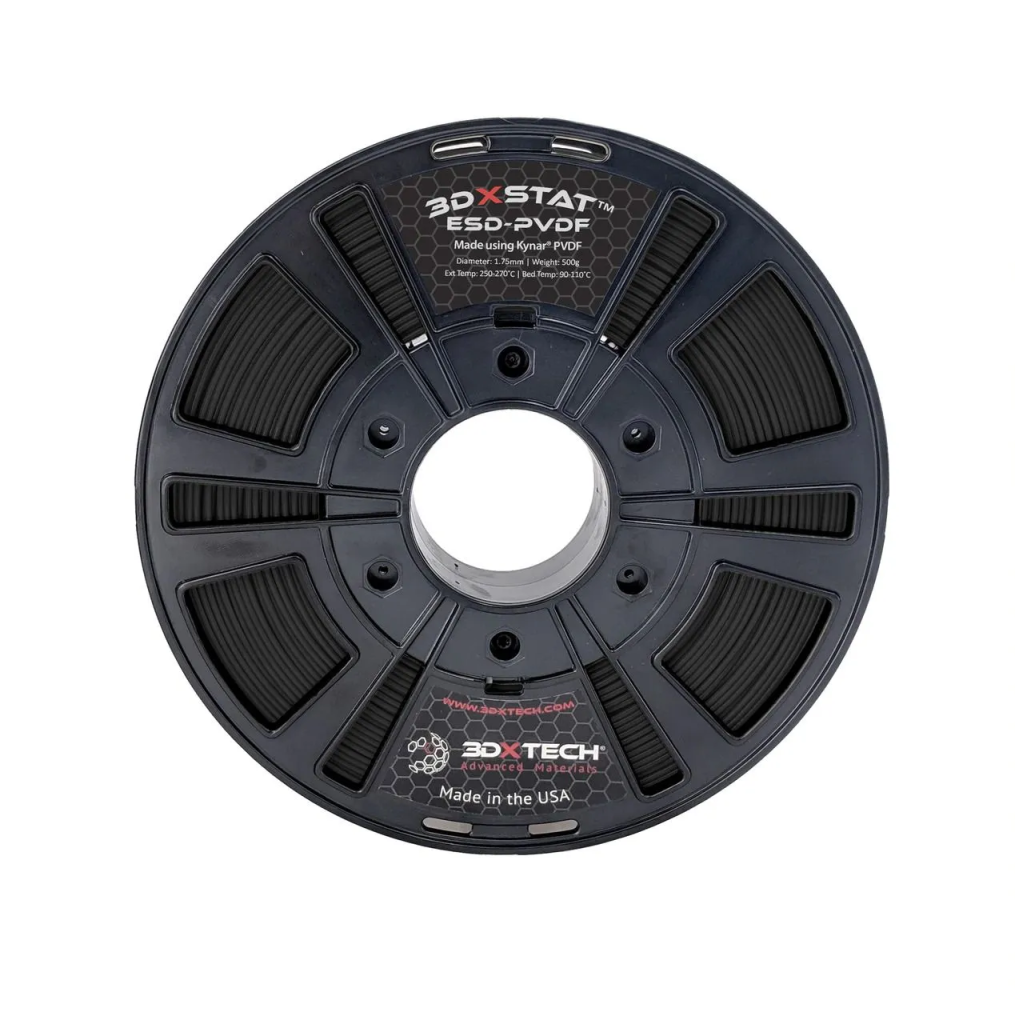
PVDF (polyvinylidenefluoride) is a polymer with unique properties, including excellent thermal stability, high strength, and resistance to extreme conditions, such as nuclear radiation.
18. PPSU: Transparent at Super High Heat

PPSU (polyphenylsulfone) is a high-performance plastic known for its excellent thermal stability, strength, and transparency.
19. Biocompatible Filaments
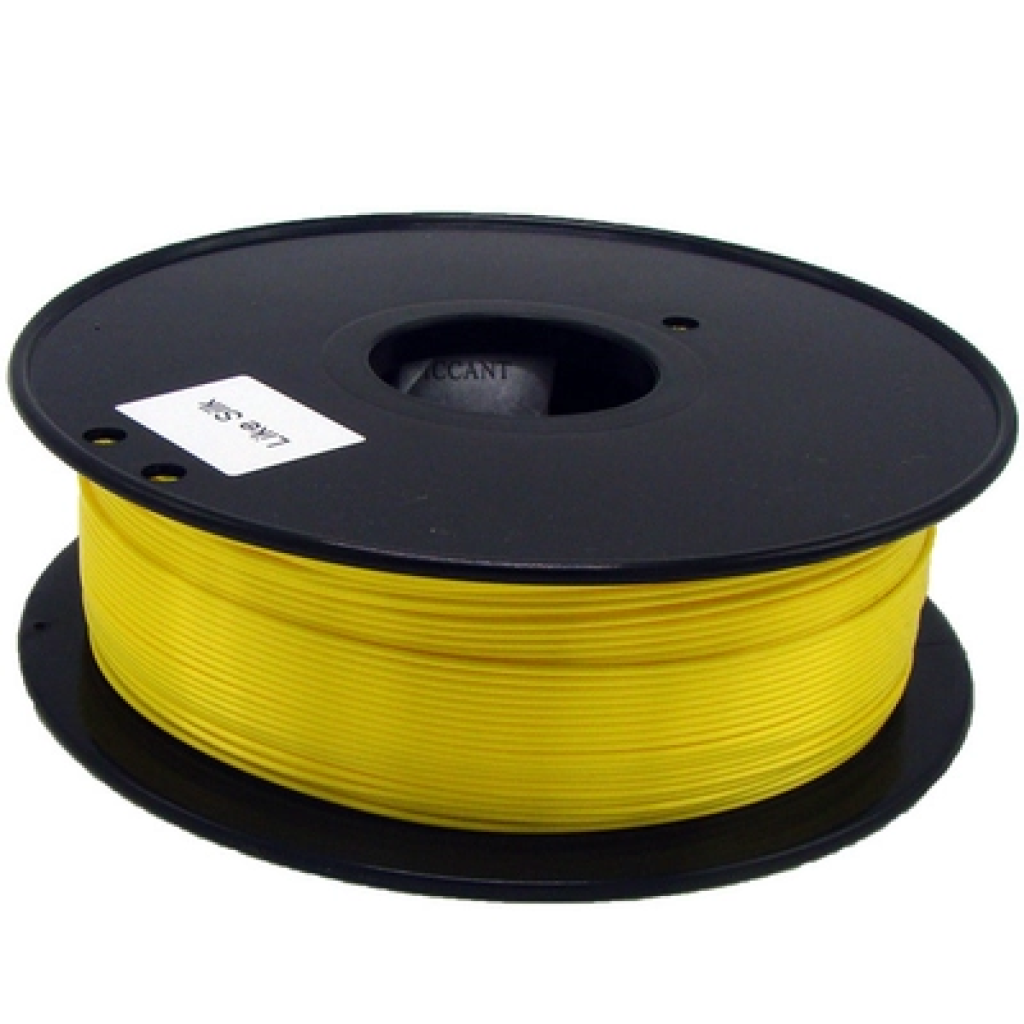
Biocompatible filaments are suitable for medical and dental applications, but compatibility with sterilization methods and chemical exposure should be considered.
RESIN
1. Standard Resins
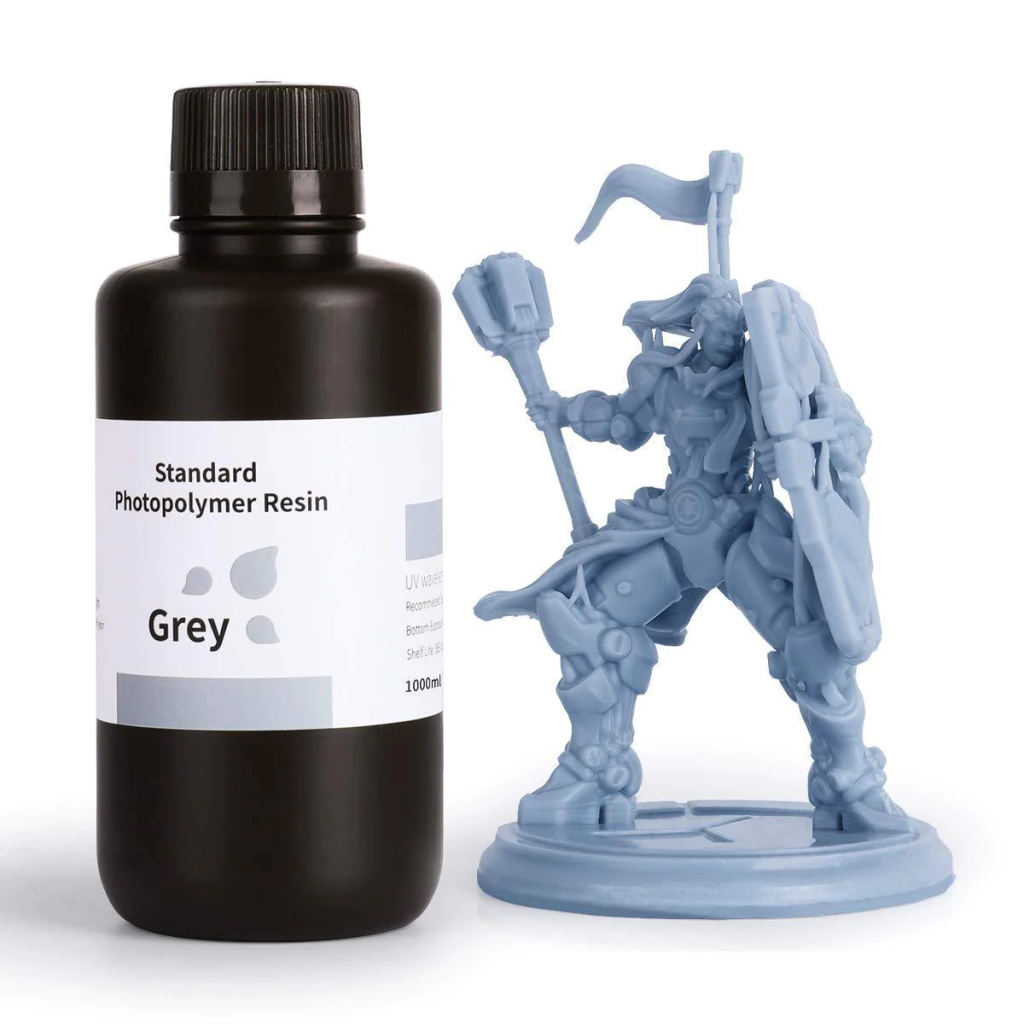
Perfect for creating conceptual models, prototypes, and visual arts. They come in various colors but can be stinky, so use them in well-ventilated areas.
2. Rapid Resins
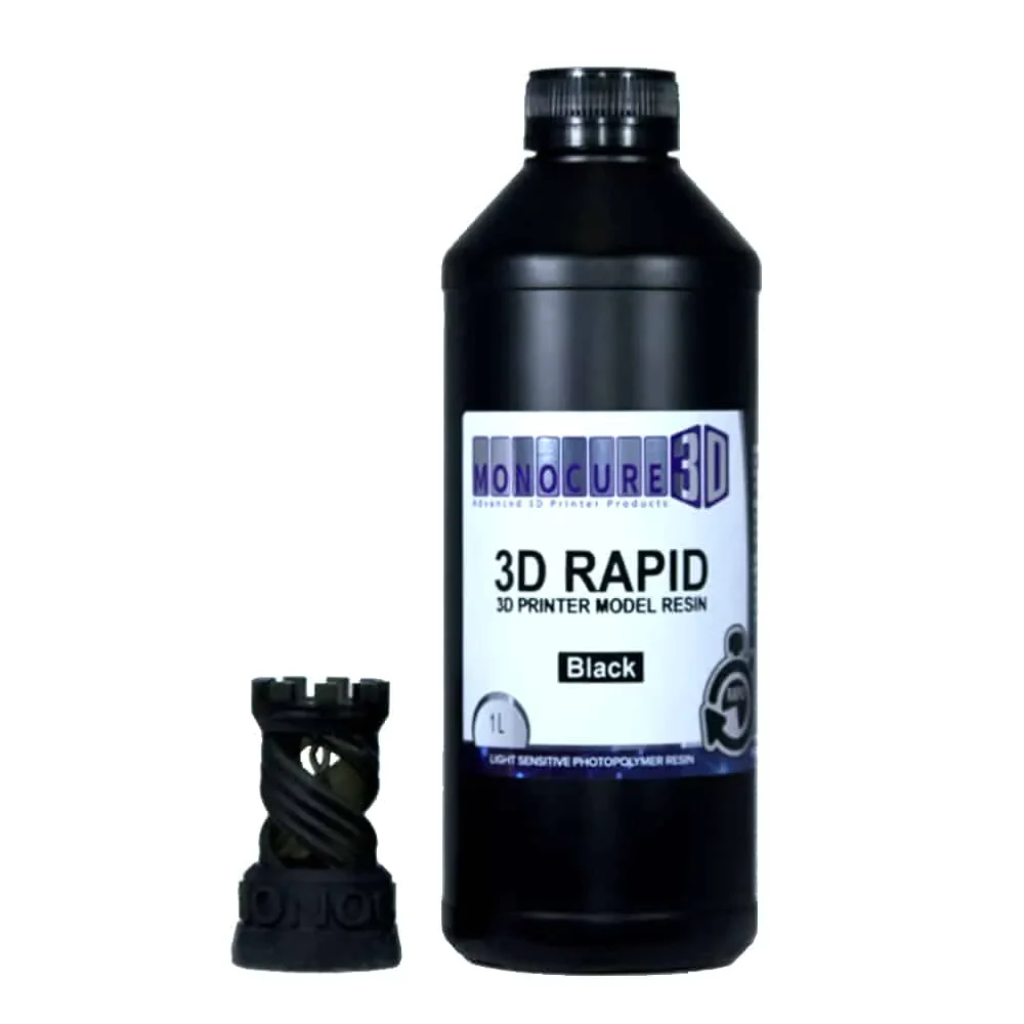
Cures quickly, preventing shrinking and deformation. Ideal for precise applications like tool or component production when time is a crucial factor.
3. Tough Resins
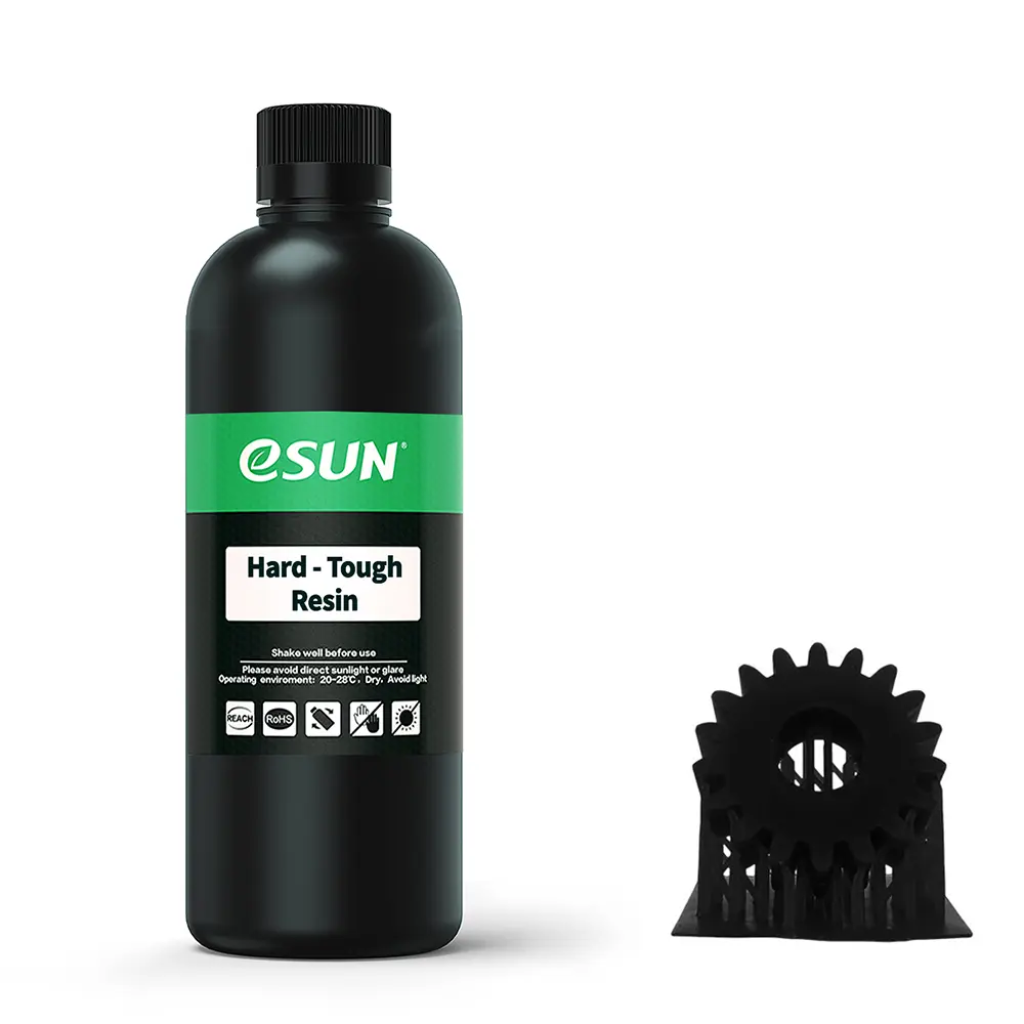
ABS-like resins with high impact resistance, mimicking the properties of Acrylonitrile Butadiene Styrene (ABS) commonly used in toy manufacturing and protective equipment.
4. Water-Washable Resins
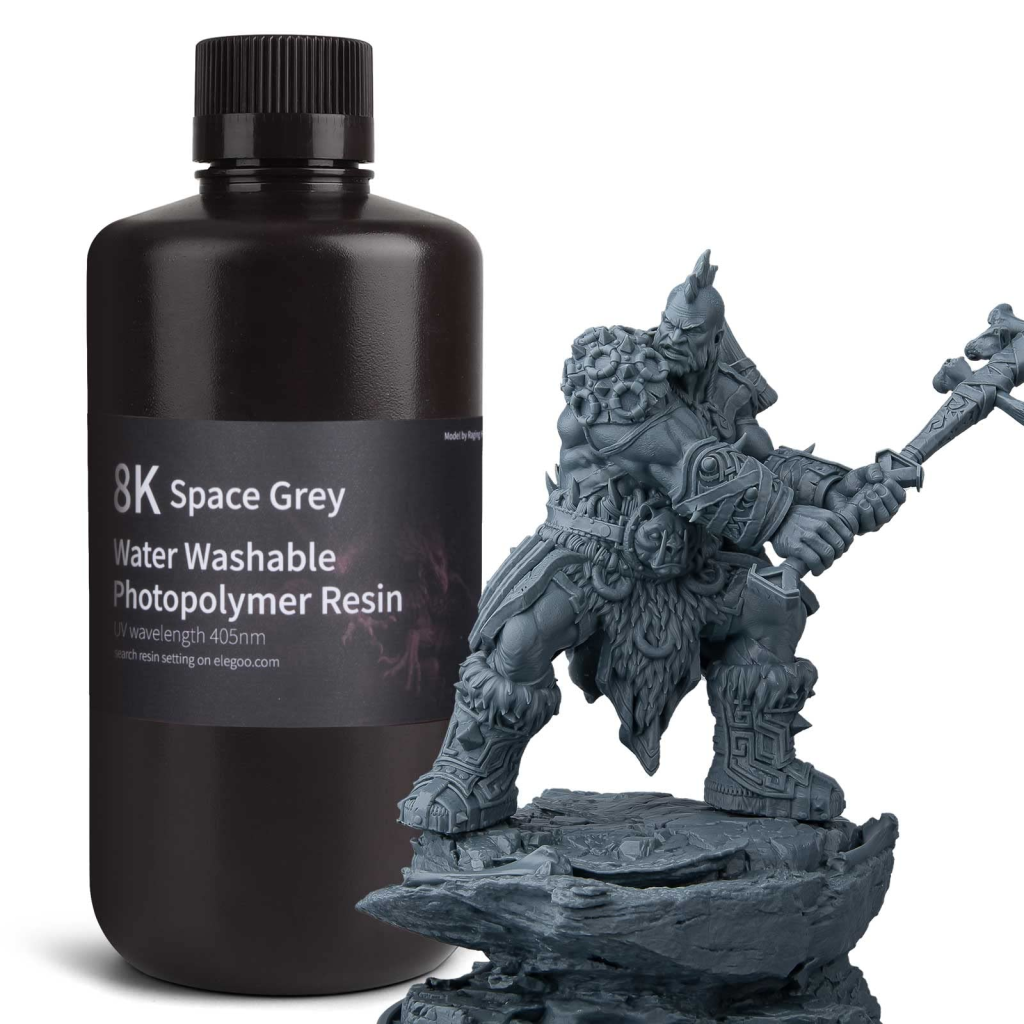
These resins are easier to handle and clean compared to standard resins since they can be washed with water.
5. Flexible Resins
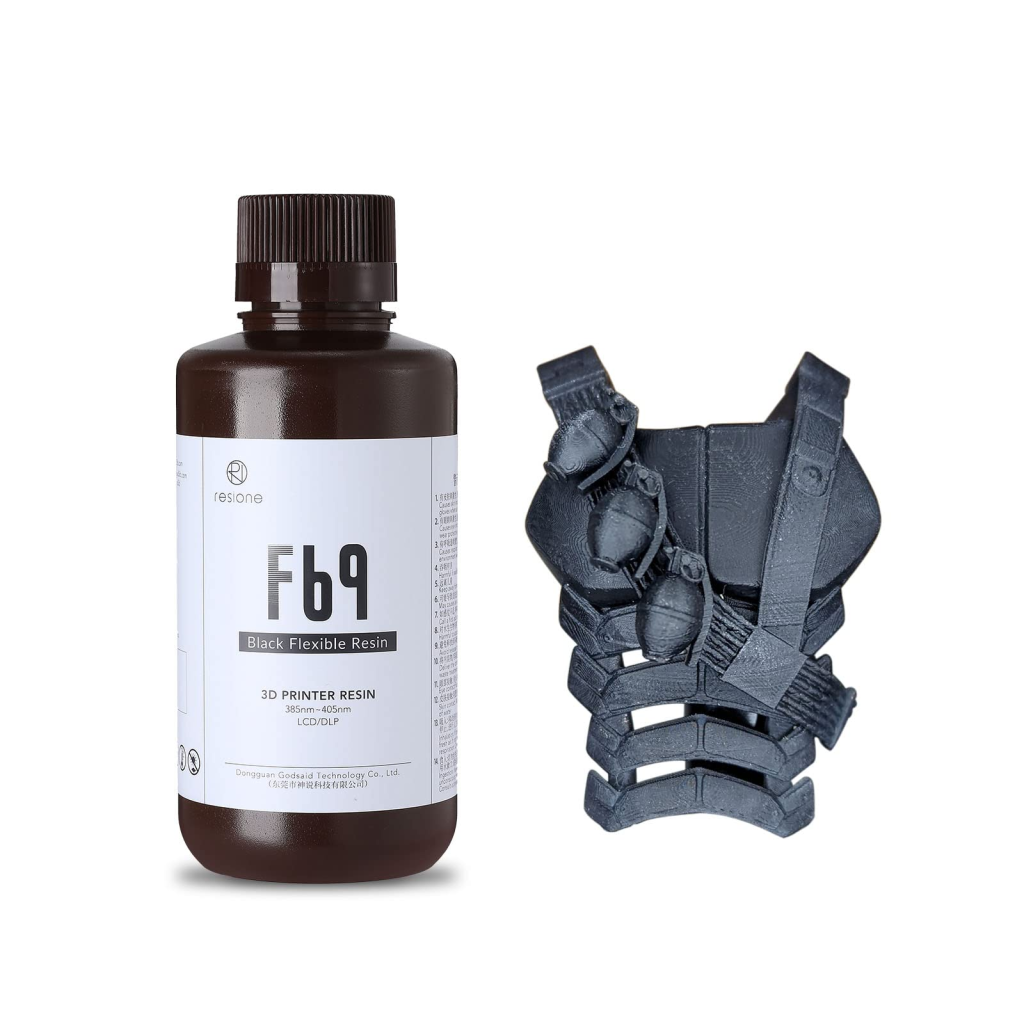
Rubber-like materials, such as thermoplastic polyurethane (TPU), suitable for applications that require flexibility and impact resistance.
6. Plant-Based Resins
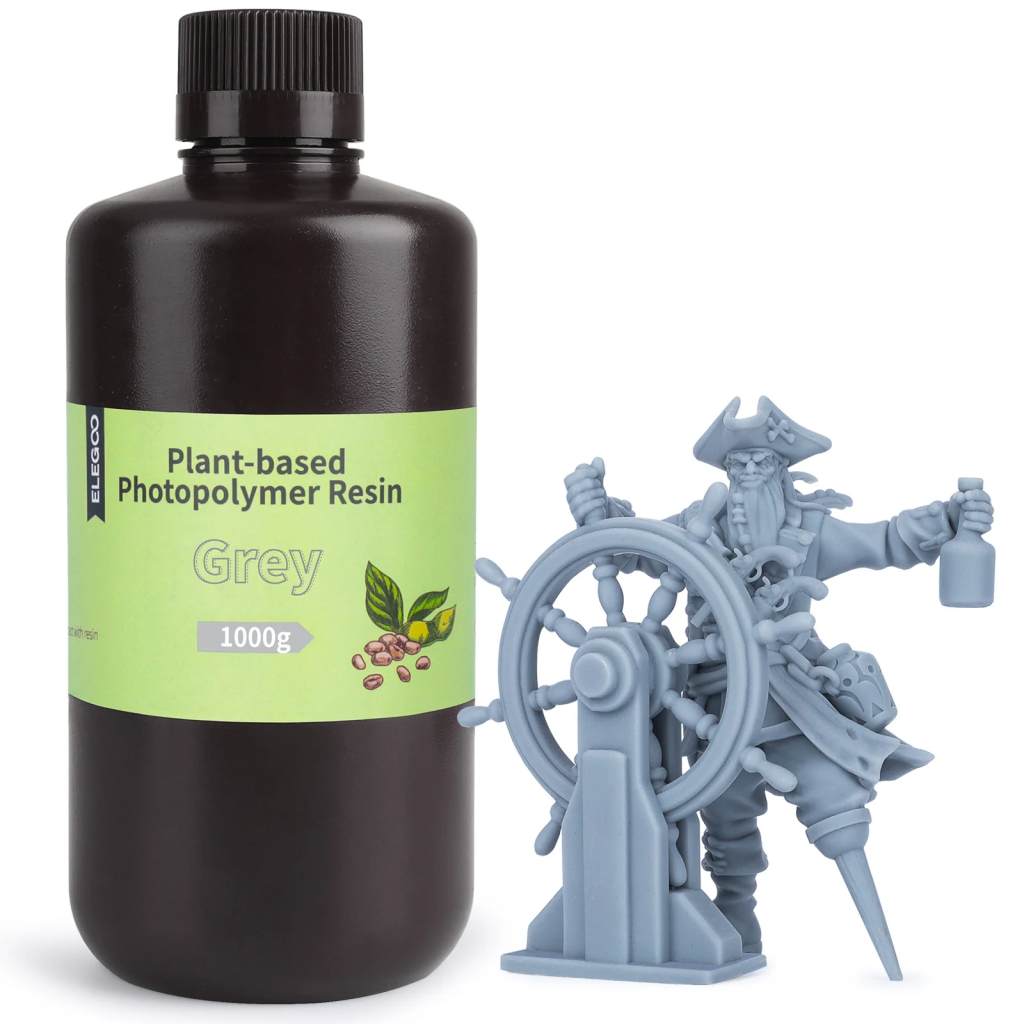
Resins made from plant-based sources, such as soybeans, offering a more environmentally friendly and less toxic alternative.
7. Castable & Wax Resins
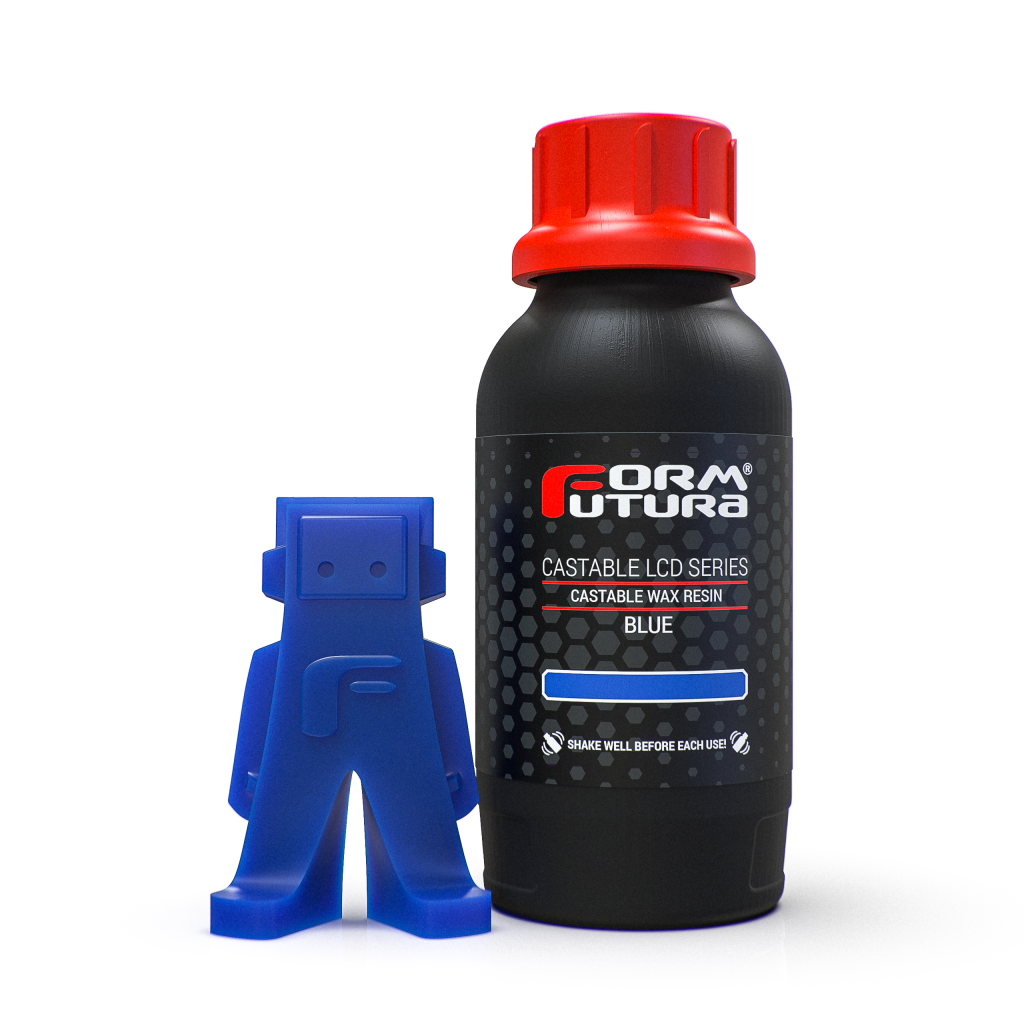
Used in combination with the lost wax method for fast and efficient prototyping. Wax models are encased in a hardening medium, melted away, and replaced with liquid metal.
8. Transparent/Clear Resins
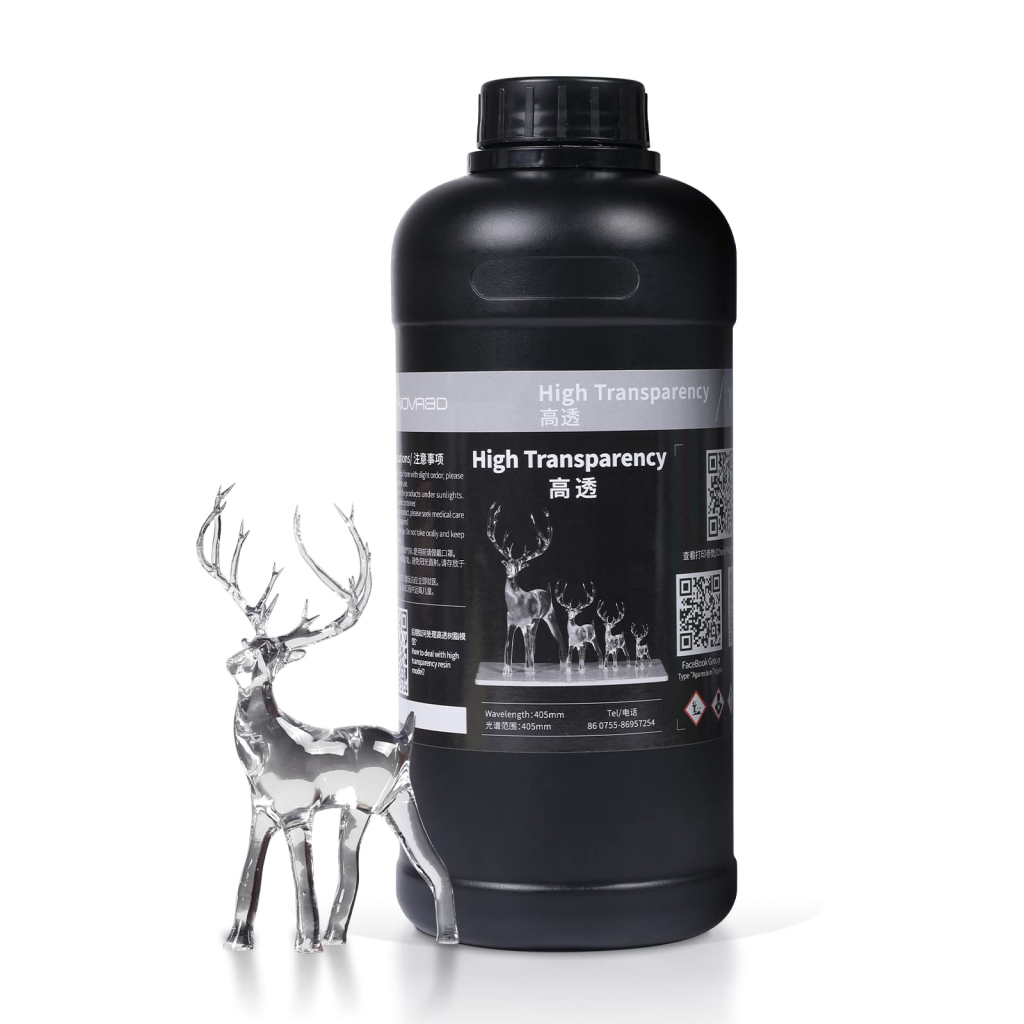
While achieving true transparency may require additional processing steps like coating, sanding, and buffing, these resins offer the potential for clear and glass-like results.
9. Glow-in-the-Dark Resin
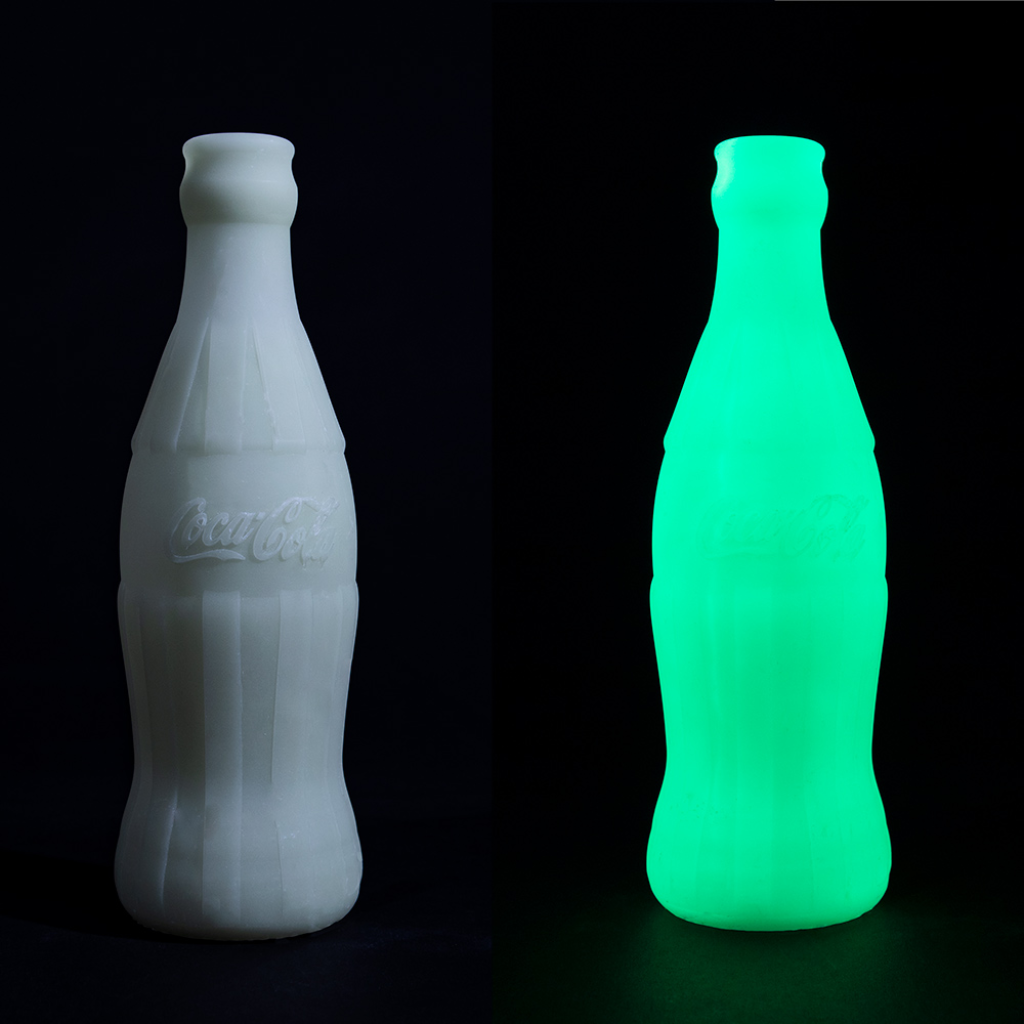
Resins that provide a cool glow-in-the-dark effect, ideal for safety reflectors or creating spooky figurines.
10. Biocompatible & Dental Resins
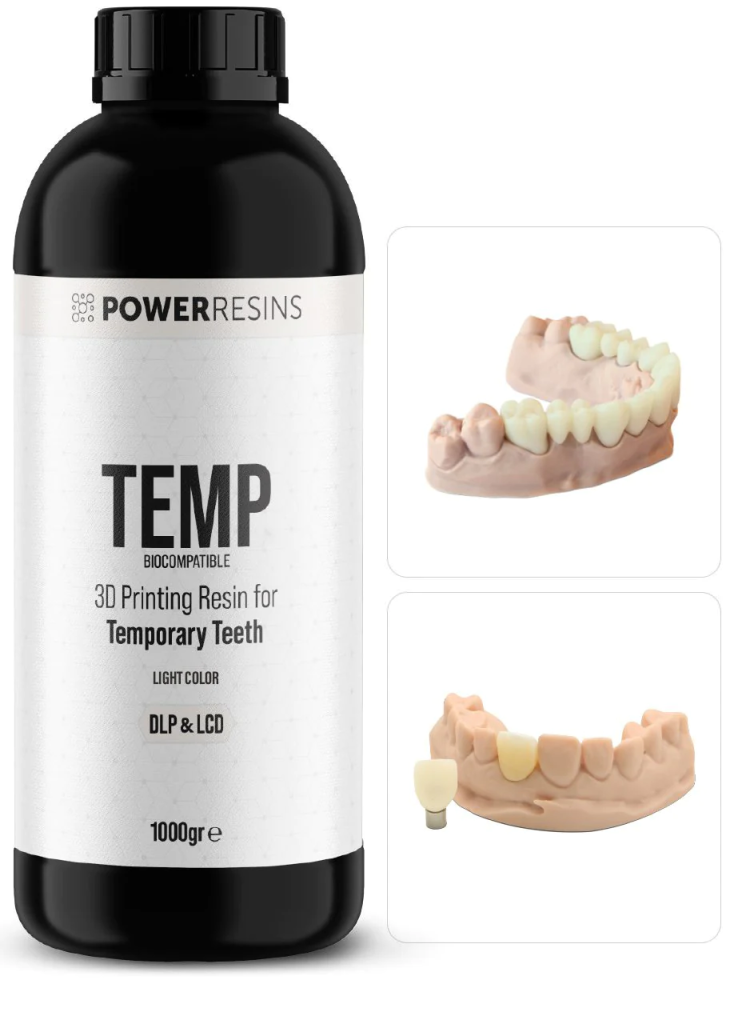
Specifically formulated and approved for medical and dental applications, including dental try-ons, implants, hearing aids, and orthopedic braces. These resins meet strict biocompatibility standards for patient contact.
METALS
1. Steel & Stainless
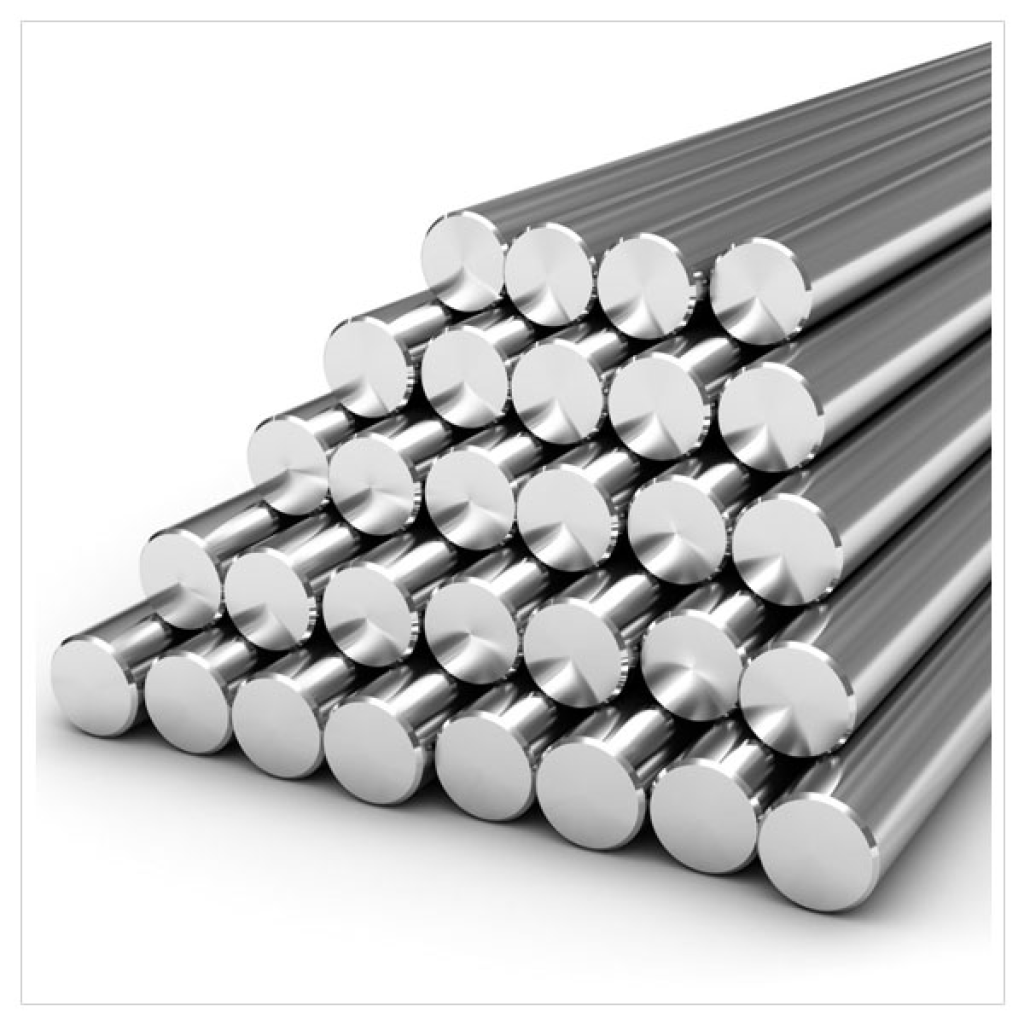
SteelVersatile, affordable, and compatible with various 3d print materials
2. Titanium
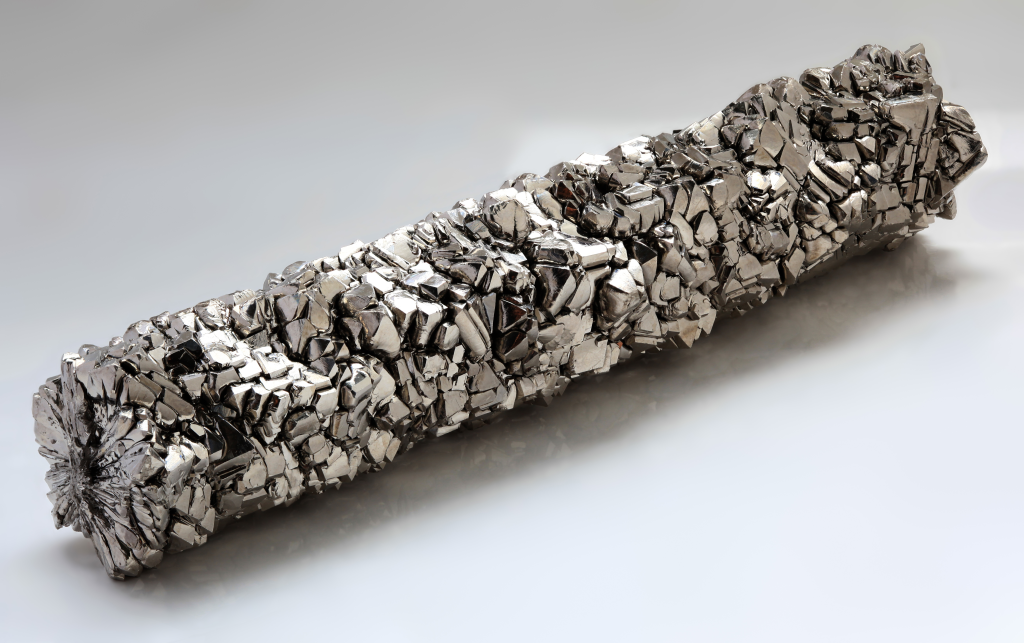
Lightweight, strong, and widely used in aerospace and medical applications.
3. Aluminum
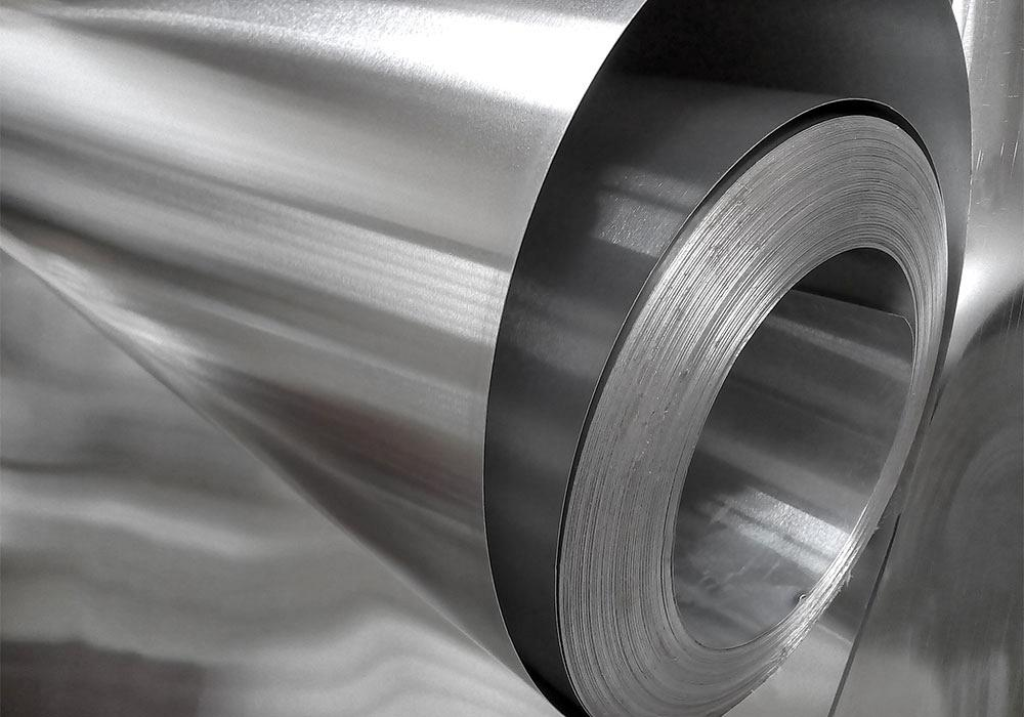
Lightweight, chemical-resistant, and offers design freedom and cost efficiency.
4. Copper
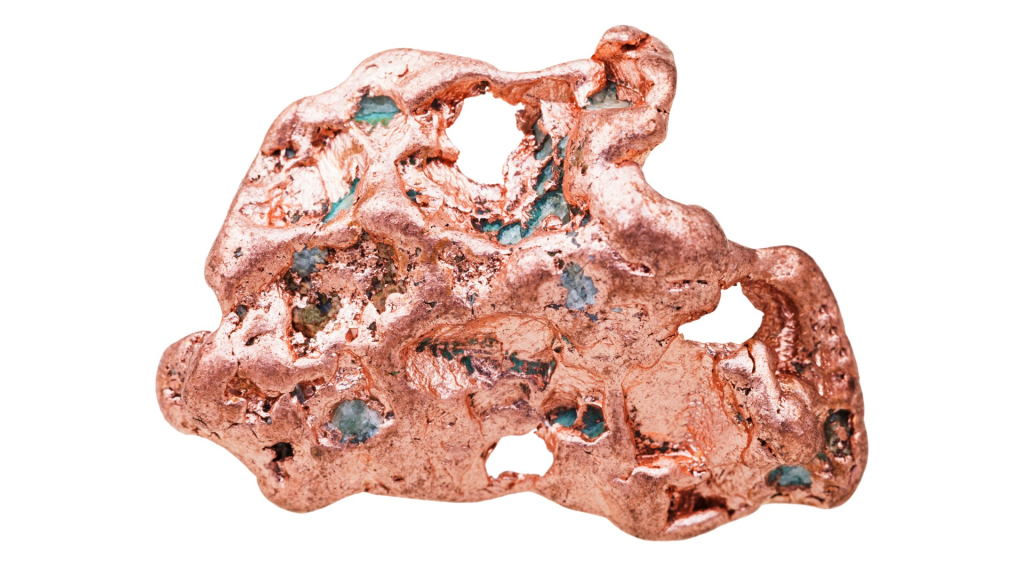
3D printable in pure form or alloys, used in sustainable technologies and available with antibacterial properties.
5. Precious Metals
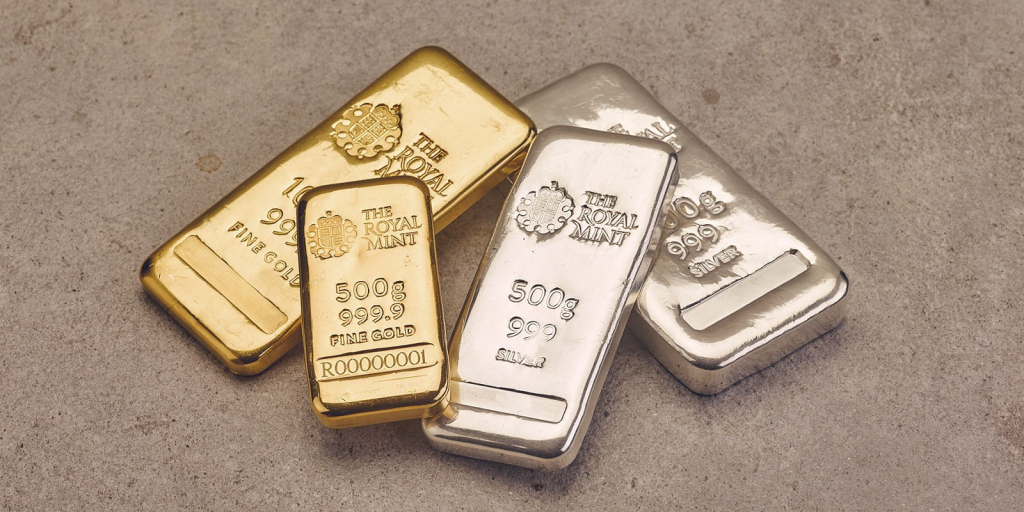
Gold, silver, platinum, and bronze can be 3D printed for jewelry and customized items.
FOOD
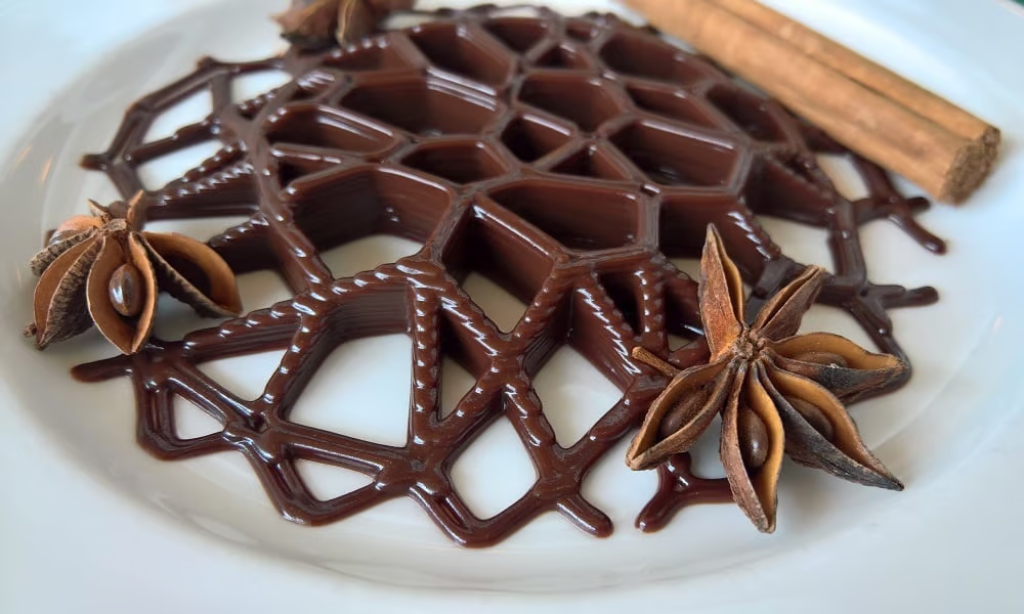
- Food 3D printing can extrude various materials, including purées, mousses, and viscous foods like chocolate frosting.
- It allows for the creation of custom three-dimensional designs with greater speed and accuracy compared to manual methods.
- Food 3D printers offer the potential to create unique and customized edible creations, setting restaurants apart from one another.
- The materials that can be printed depend on factors such as printing speed, temperature, and nozzle size.
- Some food 3D printers require proprietary materials for printing.
- While the market for 3D printed meat and meat substitutes is growing, commercially available printers for such applications are limited.
- 3D printed lab-grown meat falls under the domain of bioprinting, which involves different processes and technologies.
SILICONE
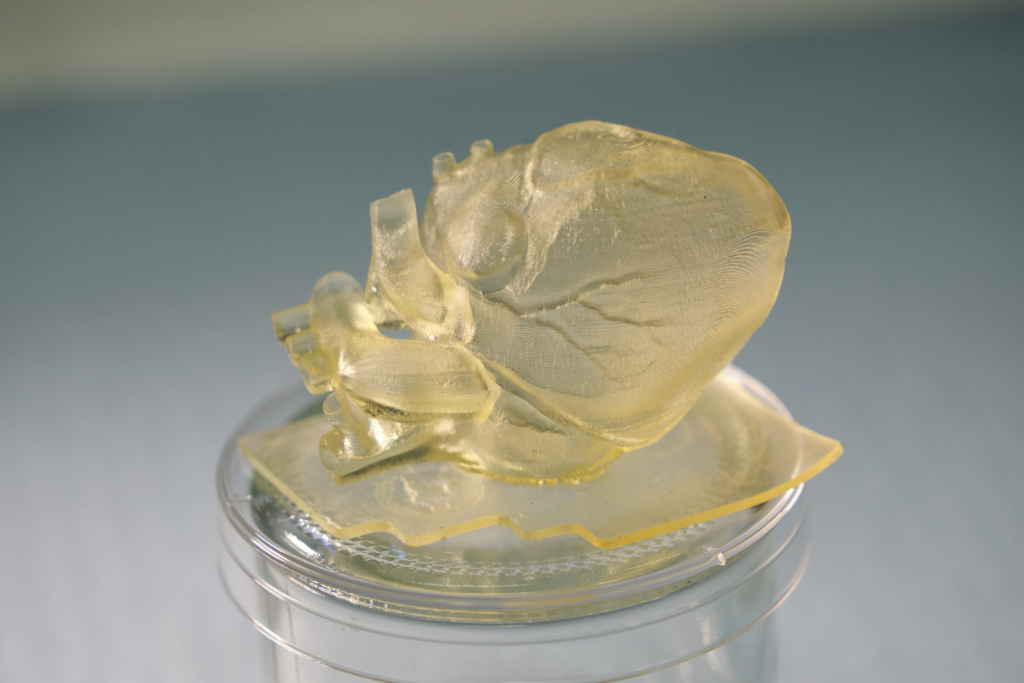
- Silicone is commonly used in seals, joints, wearable technology, and robotic grippers, typically manufactured through injection or compression molding processes.
- 3D printing silicone eliminates the need for models and molds, allowing for direct printing of the final part, saving significant time and cost.
- However, 3D printing silicone presents challenges due to its unique properties. Unlike solid polymer filaments, silicone cannot be made pliable again once solidified.
- Silicones are highly resistant to UV light and require additives to make them sensitive to light or heat, enabling polymerization and solidification during 3D printing.
- Specialized 3D printers are required for printing with silicone, although silicone-based materials (blended with other polymers) can be used on existing resin 3D printers from certain manufacturers.
- Blending silicone with other polymers in resin 3D printing allows for a wider range of applications while sacrificing some of the pure silicone’s distinct characteristics.
TECHNICAL CERAMICS
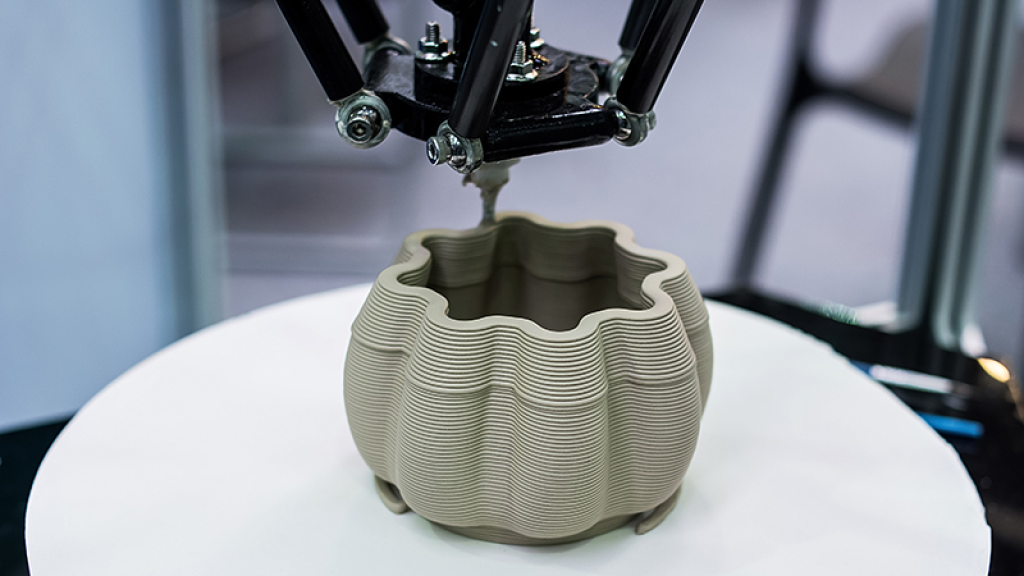
- Ceramic materials are highly valuable in high-tech manufacturing due to their unique properties.
- Technical ceramics, also known as industrial or engineering ceramics, are distinct from traditional pottery ceramics.
- Technical ceramics have diverse properties, such as exceptional strength comparable to metals, high heat resistance for extreme environments, porosity for cellular growth in implants, wear resistance for oil and gas applications, transparency exceeding glass, and electrical insulation.
- These properties make technical ceramics suitable for various applications, including semiconductors, bone implants, rocket engines, cutting tools, and more.
POTTERY & CLAY
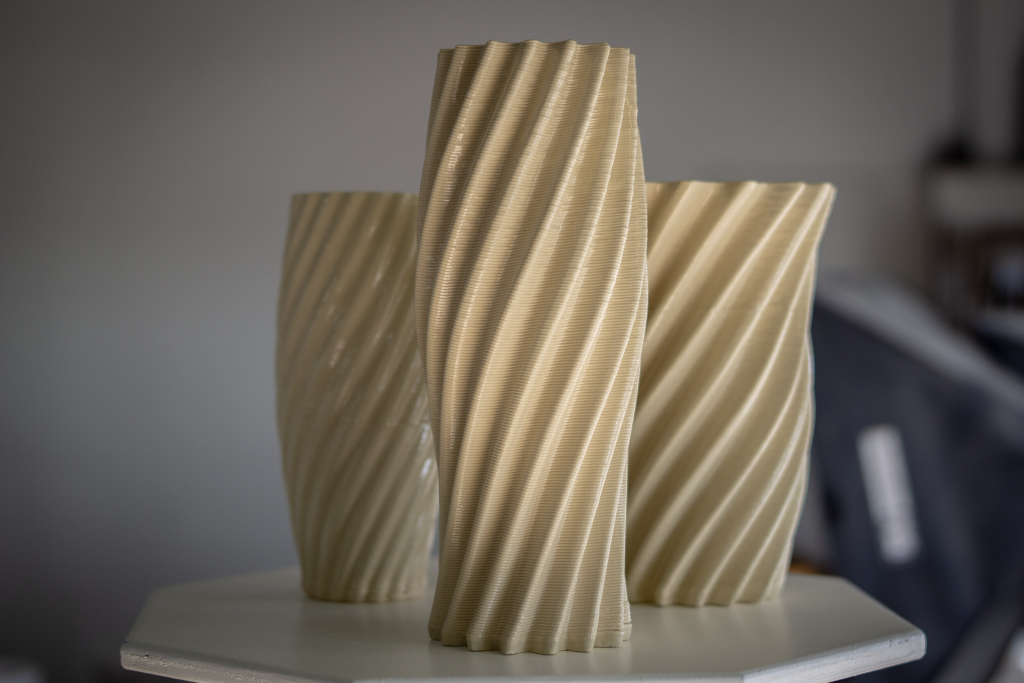
- Pottery 3D printers can utilize a wide range of clay materials commonly used in traditional pottery.
- These printers function similarly to FDM printers, extruding clay instead of plastic.
- No special or proprietary materials are needed for pottery 3D printing.
- Pottery 3D printers come in both desktop and large robotic arm versions, each with specific guidelines for the consistency of materials they can extrude.
CONCRETE & CONSTRUCTION MATERIALS
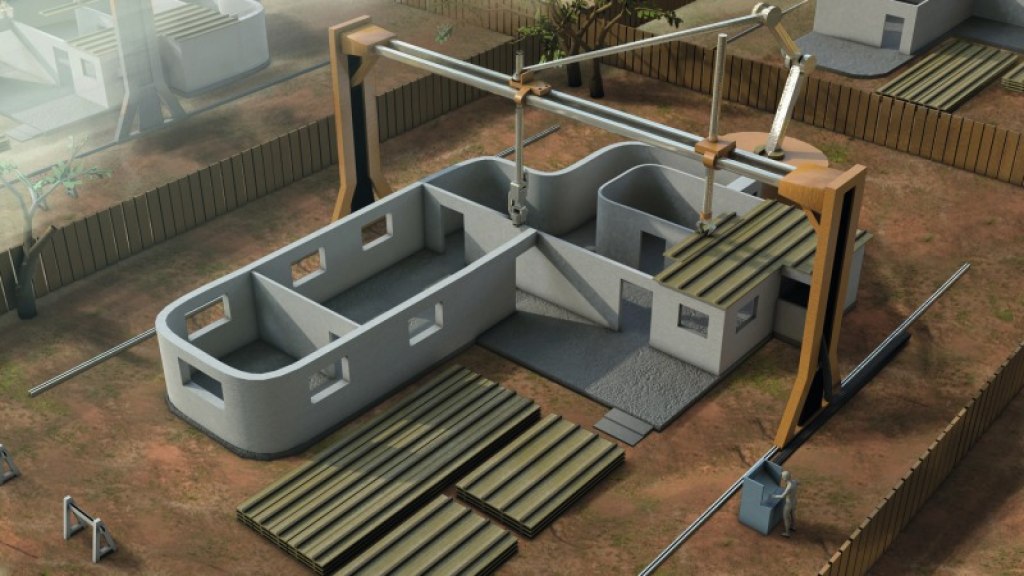
- 3D concrete printing technology is currently used for various construction projects, including homes, architectural features, and wells.
- 3D printable concrete is typically a mixture of cement-based materials, including super-plasticizers and fibrous additives for enhanced strength and faster drying.
- The material blends used in 3D concrete printing are formulated to optimize printability and specific purposes, such as housing walls or decorative architectural elements.
- Manufacturers often develop their own proprietary material blends, tailored to their 3D printers or in collaboration with partners.
- Currently, the cost of these proprietary material blends is generally higher than standard construction cement, but this may change in the future.
- Some notable proprietary material blends include Icon’s Lavacrete and CyBe’s CyBe Mortar.
- Recently, a test building was 3D printed using standard concrete by Mexican cement company Cemex, the German University of Technology in Oman, and printer maker COBOD.
BIOMATERIALS
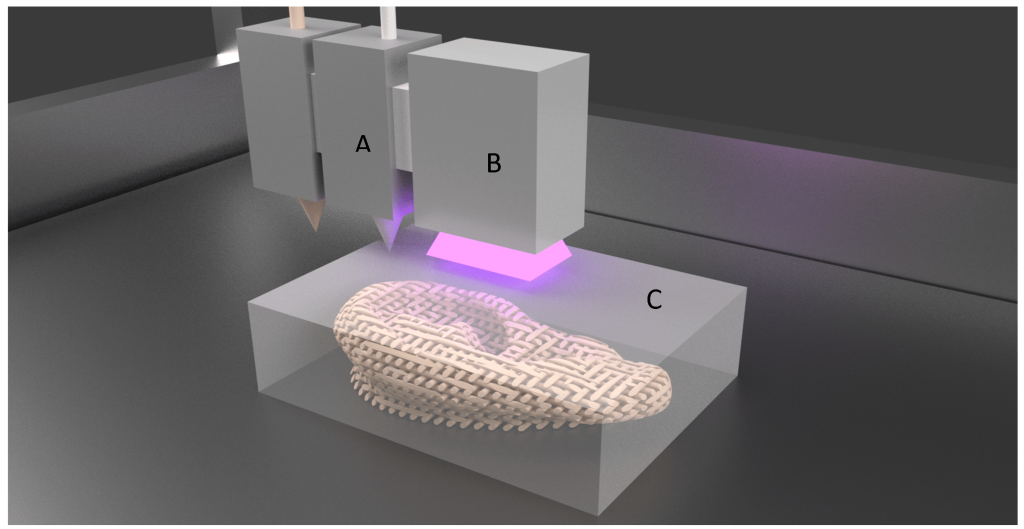
- Bioprinting is a type of 3D printing that utilizes living cells and biomaterials to create artificial living tissues for medical applications.
- Bioprinters use a material called bioink, which consists of cells and a biopolymer gel that acts as a 3D molecular scaffold.
- The bioink allows cells to attach, spread, grow, and proliferate, enabling the formation of engineered live tissues.
- The biopolymer gel in the bioink provides protection to the cells during the printing process and serves as a supportive structure for tissue development.
- Bioprinting has potential applications in tissue engineering, where it can help create complex structures like bone tissue and blood vessels.
- It also finds use in drug testing and development, allowing researchers to create realistic tissue models for studying the effects of drugs.
- While the ability to 3D print functional organs is still a distant goal, bioprinting shows promise in advancing regenerative medicine and personalized healthcare.